HEMS TECHNOLOGY
The basic principle of HEMS technology is that combustion of fuel such as petrol or diesel in an internal combustion engine can be enhanced by the addition of a small quantity of hydrogen with the fuel and air. In our system hydrogen is injected into the air inlet of an internal combustion engine. Hydrogen is stored on the vehicle and injection into the engine is controlled by a patented electronic system that responds to the engine parameters.
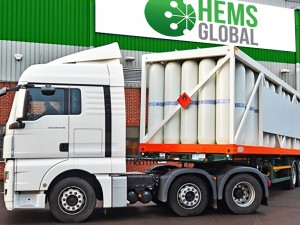
The basic principles are the same for all Internal Combustion Engines
STROKE 1 | INLET (SUCTION) |
A small quantity of hydrogen gas is drawn into the cylinder along with the air via the inlet system of an internal combustion engine. |
STROKE 2 | COMPRESSION (SQUEEZE) |
Hydrogen mixes with the air and fuel, and as the piston goes up, the fuel+hydrogen/air mixture is compressed. On a diesel engine, the heat and compression ignite the fuel mix. On a petrol engine, a spark ignites the fuel air mixture. In a jet engine, the ignition is self sustaining after starting. |
STROKE 3 | POWER (BANG) |
When the mixture is ignited by compression (Diesel) or a spark (Petrol or LPG/CNG) the flame burns at a much faster rate than in the absence of hydrogen. This means that the combustion process is faster and is much more efficient. As the combustion is faster, there is more time for the fuel to burn completely. |
STROKE 4 | EXHAUST (BLOW) |
Most or all of the fuel is burnt. This reduces the unburnt fuel or HC content of the exhaust. It also reduces the level of carbon monoxide in the exhaust gas and, because combustion of hydrogen-enhanced fuel is fast, the combustion temperature is lowered, resulting in the production of fewer oxides of nitrogen NOx. As unburnt fuel causes black smoke as well as diluting and contaminating the engine lubricating oil, these effects are also reduced. |
The HEMS system comprises a cylinder of hydrogen is mounted on a vehicle at a convenient location, and a controller mounted between the cylinder and engine. There is very little interference or adaptation required to the existing vehicle systems. The driver or operator has a master switch to turn the hydrogen system ON and OFF, however, the system is fully automatic when turned ON. In summary:
- Hydrogen gas is added to the air-intake and regulated by the HEM’s controller over the entire engine operating range, including idle.
- The HEMS system will automatically shut off whenever the engine stalls, there is a hydrogen leak, whenever the system pressure is low and whenever the controller detects a fault internally.
- When the Hems System is ON, the hydrogen will not flow until the engine is actually running. The engine reverts to the original fuel (diesel, petrol, LPG etc) when hydrogen runs out or is turned off.
- HEMS System is applicable to any internal combustion engine application (buses, trucks, gas turbines and power generators).
Whilst the gaseous stored hydrogen system (the current HEMS technology) provides an optimal method of control and delivery of hydrogen to the engine, the ability to safely mount cylinders to provide enough hydrogen for the distances travelled by some of the heavy freight, trains and marine vessels is restricted by the available space and the current level of hydrogen infrastructure available in Australia. This limitation will be overcome by new Hems Technology being developed.
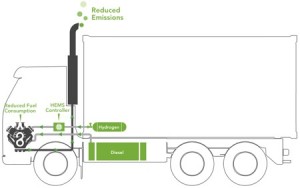
HEMS Water Fumigation System (WFS)
HEMS International is working on a range of new technology that will reduce NOx emissions dramatically and increase engine power. The WFS system involves water fumigation to provide additional cooling of the combustion chamber. This reduces the temperatures at which NOx forms.
Oxides of Nitrogen (NOx) are produced at high cylinder temperatures. A fact of the internal combustion engine is that when the engine is operating at its most efficient, the cylinder temperatures are at their highest. As engine manufactures improve the efficiency of their engines by increasing compression ratios and cylinder temperatures, they are hamstrung by the NOx. This is why the new vehicles now are fitted with catalytic converters and exhaust recirculation Systems.
The current HEMS System does reduce NOx due to the faster burn rate of fuel achieved by the injection of hydrogen into the engine. The addition of the WFS further reduces the NOx.
Fleet Operations Monitoring
The R&D Team are completing the development of a fleet operations monitoring system that remotely monitors the engine operating parameters on vehicles using mobile technology and Satellite tracking.
The HEMS System can be adapted to provide a “GREEN BAND” prompt for the driver to follow.
The GREEN BAND system will illuminate an amber light whenever the vehicle is being operated with a heavy foot. The idea is for the driver to keep the light OFF. Research has shown that one of the main causes for high fuel consumption is that the engine is often forced to operate at high boost to achieve rapid acceleration.
The HEMS System meets the following standards
AS/NZS 2739
Technology
The technology was not available to control the flow of hydrogen and was the stumbling block for everyone wanting ot take advantage of the properties of hydrogen in an internal combustion engine.
Our specialists designed a logic based controller and software to create a Control and Delivery System for hydrogen gas injection that is used as a catalyst in an engine.
This is ground breaking new technology which is now driving our Research and Development team to investigate and develop associated systems and improvements.
Industry Acceptance
The transport industry and regulators were not familiar with hydrogen when used as a fuel catalyst. We discovered that Hydrogen was not even listed in the Australian Government’s Gas Act as a gas. The properties of Natural Gas and Hydrogen are similar – they are both flammable gasses, rise vertically in the air when released and have similar system pressures. As such, the system designers chose the guidance of the AS/NZ 2739 Standard as the basis for the system design. Hems International have actually exceeded the safety requirements of this standard!
CFS International have certified the HEMS System installation as compliant with the AS/NZ 2739. This has been accepted by the Australian (NSW Roads and Maritime Services) Road Transport regulators as an approval to operate the vehicle on Australian roads.
Component Quality and Standards
Some component manufacturers promised functionality which was not, in fact, there.
We tried many different manufacturers of the components to be used in our system. There were many failures, either by not meeting our expected standard in the first place or failure when in test.
We finally found component manufacturers that delivered what was promised. We finally had components that were consistent in quality and met the required standards.
Approved Standards and Design Rules
As mentioned earlier, as the Australian Gas Act did not recognise hydrogen as a gas, there were no applicable standards available for hydrogen.
There were generic International standards and Australian Standards were only available for Liquid Petroleum Gas (LPG) and Compressed Natural Gas (CNG) in Vehicles. As Hydrogen and Natural Gas have similar properties, we used the CNG Standard (AS/NZS 2739) as the basis for our design. It is to this standard that our installation has been certified . A vehicle fitted with the HEMS Diesel Reduction System is therefore permitted to be operated in the road.
No Australian Design Rules are compromised and all standards are complied with. However, with the introduction of the Hydrogen Fuel Cell technology, EC-79 and UN R134E have been developed in Europe for the use of Gaseous Hydrogen in Automotive Transport. We have reviewed the AS/NZS 2739 and due to the Australian Standards being of the highest in the world, the EC-79 and UN R134E are complied with within the AS/NZS 2739. Additional certifications are in progress for all installations.
Public Beliefs, Facts and Fallacies
There were variations of fact and fallacy regarding hydrogen.
FALLACY – Everyone remembers the old news stories of the Hindenburg Airship disaster on the evening of May 3, 1937.The hydrogen caused the airship to burn.
FACT – What is now becoming common knowledge is that it was NOT the hydrogen that was burning. When hydrogen burns, it is with a clear flame! The fire started by static electricity and was fuelled by the dope (paint) covering the airship skin. In fact, they were able to recover some of the bags of hydrogen once the fire was out. Hydrogen is flammable. This is very true, which is why we use it. It must be remembered that hydrogen burns very fast; so fast that in most cases the surrounding combustible material has not been heated enough to actually ignite.
SAFETY
The HEMS system has been designed to minimise risks of leakage.
- We have leak detectors in various locations to automatically shut the system down if there is a leak.
- All connections and components are approved for use with hydrogen
Other systems may be available that do not have an accurate hydrogen flow control mechanism. These do not deliver consistent results. The Hems system uses a patented control and delivery system to ensure consistency of hydrogen flow.